What is CNC Manufacturing & what are the different types of CNC processes?
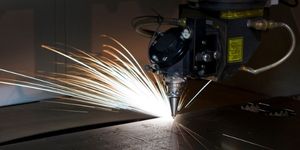
August 11, 2022
CNC manufacturing has been an essential staple of many industries and manufacturing plants since emerging in the 1940’s, when the first numerical control machines were introduced. The technology revolutionised the way we create three dimensional parts replacing handcrafted techniques, increasing precision, consistency and enabling high volume production for increased profits. CNC manufacturing marked the start of industrialisation and today involves incredibly intricate, modern technology that is fully automated to produce stunning results. Let’s explore CNC manufacturing, processes and its advantages further:
What is CNC Manufacturing?
CNC manufacturing is automating the creation of parts via the use of a computer. CNC is an acronym that stands for Computer Numerical Control; machine tools, programmed via microcomputers with specialist software installed, automate a variety of tasks involved in manufacturing a 3D object. CNC machining is a subtractive manufacturing process which removes cutting or removing material from a workpiece, in contrast to an additive manufacturing process like 3D printing.
How Does CNC Manufacturing Work?
CNC manufacturing technology works using a machine, operated by a computer and software, with a cutting component that mills and turns against a solid block of material. The cutting tool will transform the workpiece or blank into the design which was originally programmed into the machine. A 3D design is programmed by a person using CAD (computer aided design) software, that is then converted into a CNC programme (G code). The machine is set up with the programme, cutting tool and work piece – this could be metal, plastic, wood, glass, foam and composites, and then works autonomously until complete.
What Are the CNC Processes?
CNC Drilling
The CNC drilling process involves a cutting machine with a multi point, 3 axis drill bit that cuts cylindrical holes in a blank. The CNC machine forces a rotating drill bit, chosen for its diameter in line with the precision required for cutting, perpendicularly to the plane of the blank’s surface in order to create holes.
CNC Milling
The CNC milling process involves a cutting machine with a 3 or 5 axis rotating multi point cutting tool that removes material from the blank. The machine’s base moves up and down to create the depth of cutting whilst the tool, attached to a spindle, cuts across the blank by moving along its 3 linear axes. CNC milling is the most common CNC process due to its high accuracy, ease of set up and operation, with low start up machining costs. However, if the 3D design has complex geometries there may be areas the tool cannot reach. Learn more about Dudley Industries 5-axis CNC milling machine.
CNC Turning
The CNC turning process involves a cutting machine with a rotating chuck that holds the blank, whilst the cutting tool is fed into it to remove material. It creates the 3D shape by tracing the outer and inner shapes, but it only moves outward and lengthwise and does not rotate. This limitation makes the CNC process only suitable for objects with rotational symmetry thus it’s often used as a second step, to create additional rotational features required. However, CNC turning can mass produce objects at a great speed making manufacturing costs lower than CNC milling.
What Are the Advantages of CNC Machining?
CNC machining has many advantages due to its automation and precision abilities – let’s explore them further:
- CNC machining can be executed on a wide range of materials, including metal, plastic, wood, glass, foam and composites, making its uses, capabilities and industry applications endless.
- It can execute both tiny, intricate projects up to large pieces.
- CNC machining can execute intricate, complicated designs with ultimate precision (important for industries like aerospace).
- It can produce on mass and in short time scales.
- CNC machining can execute accurate, products with consistent quality – every piece is identical.
- It’s cost effective at producing complex parts with no human error to consider (unless made at the design stage), resulting in less rework and scrap material.
- CNC machining allows for quicker assembly of products.
- CNC machining eliminates the need for human intervention, leading to enhanced safety and less accidents.
- Working around the clock a CNC machine can work consistently 24 / 7 / 365.
What Can CNC Machining Be Used For?
CNC machining can be used for a variety of projects across all sectors. This could include but not limited to instrumentation and laboratory cabinets, transport and infrastructure, controls such as audio mixing desks, medical equipment through to architectural designs all of which require a high level of precision and accuracy for the product to fulfil its brief. Common industries include automotive, aerospace, electronics, transport, construction and product development.
CNC machining is used commonly for metal objects. Electronics, railway parts, car, boat and plane parts and so much more all require precision accuracy, and without it, many of our everyday items couldn’t be relied upon.
CNC machining can cut many metals including titanium (aircraft, biomedical and military parts) stainless steel (pipes, kitchen components) aluminium (car frames, laptops), brass (electronic hardware) and carbon steel (gears nuts and mechanical parts).
Here at Dudley Industries, we have the latest CNC machining technology which enables superior cutting performance of stainless steel, copper, brass, aluminium and most other exotic metals and alloys. We operate three flat-bed lasers including one state of the art fibre laser. We can work to a tolerance of 0.1mm on sheets up to 3000mm x 1500mm. We download production plans directly into our CNC machines, and the CNC nesting software ensures optimal material usage and minimal waste material for prime CNC sheet metal fabrication.
How Dudley Can Support You with Your CNC Manufacturing needs
Dudley can support you with your CNC manufacturing needs via our CNC metal cutting and tooling facilities. We offer superior contact manufacturing for any sheet metal project or product with a dedicated service for concept to large scale product of metal solutions.
We are world renowned CNC designers and manufacturers of innovative metal products. With over 80 years’ experience and ISO 9001:2015 accreditation, contact our inhouse consultancy service with your requirements on 01253 738311 or email sales@dudleyindustries.com